Completeness check on the ball bearing.
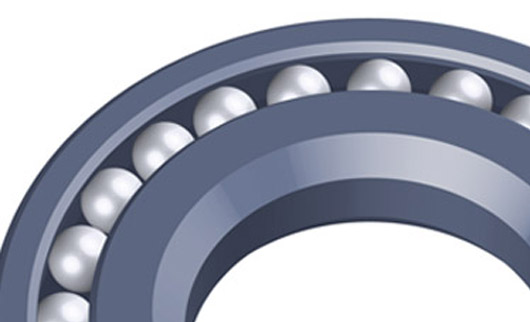
In a manually loaded assembly line for the production of high-quality ball bearings, the presence of all balls should be ensured. The special feature: ball bearings with 40mm-280mm Ø and particularly small gaps between inner and outer ring. Due to the use of ceramic balls a reflected light inspection is not possible due to missing reflections. The design of the system requires special approaches in terms of optics and part transport. Due to the narrow gap, recognition in transmitted light is only possible with a telecentric lens. For the part size of approx. 300mm Ø, such a lens can be optimally used in combination with a line scan camera due to its design. Furthermore, the parts must not make any unsteady transport movements under the line scan camera, as otherwise the small gaps cannot be detected or pseudo faults occur. Therefore, only a roller conveyor with small roller gaps can be used. Testing is possible for a large number of variants by adjusting the parameters.
Seamless surface inspection of fuel pumps.
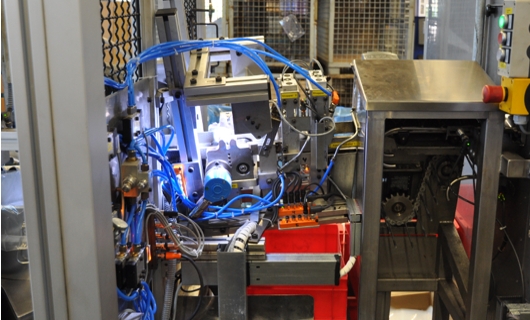
Fuel pumps work in secret for the life of a car. This requires a faultless surface of the pump housing. In order to guarantee this, Präschu Umformtechnik has opted for an in-line inspection system with automatic surface inspection of the pump housing. The optical inspection system that checks the parts after deep drawing can ultimately also detect tool defects and tool adjustment problems. The tubes are washed after deep drawing and then presented individually and in the correct position via a slide with stoppers of the image processing. A roller mechanism rotates the parts under the camera around their longitudinal axis by 380°. The CV-600 system records the camera images with a line scan camera and high resolution and evaluates them automatically. In order to compensate for process- or material-related variations in the appearance of the housings after deep drawing, the CV-Inspect software uses locally adaptive methods to compensate for the variations in brightness. The sensitivity of the error segmentation and the response limit can be parameterized by the operator. Errors starting at a size of 0.2mm for ejection of the part. Inspection regions and exclusion areas can be set flexibly. Good parts go directly to packaging.